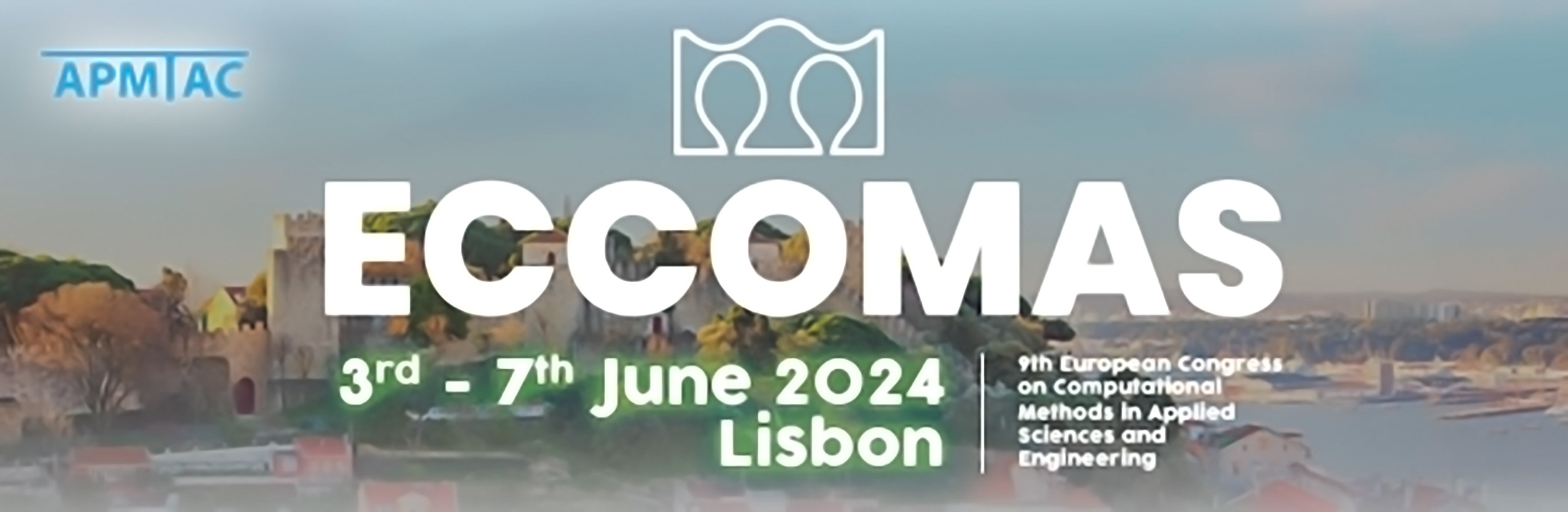
Numeric Comparison of Hydraulic and Pneumatic Flow Forces and Velocities in a Proportional Solenoid Valve
Please login to view abstract download link
Hydraulic proportional solenoid valves are designed to control the flow rate of a fluid passing the valve, based on the electric current applied to the solenoid. The electric current governs the spool position, which in turn opens and closes an orifice that allows the flow to pass. The functional test of this valve type using liquid fluids such as hydraulic oil is expensive, requires frequent exchange-service and contaminates the test object before shipping it to the customer. Conducting the test with an airflow instead would diminish or eliminate these undesirable effects. Of course, a pneumatic testing procedure is only valid if all testing criteria originally defined for hydraulic testing are still met reliably. To evaluate this approach, we have carried out experiments and full 3D simulations for both hydraulic and pneumatic flow. For the experimental validations, identical test stands holding a test valve are each connected to a hydraulic or to a pneumatic source. To ensure comparable results, the pressure drop is set to be identical and constant for hydraulic and pneumatic flow. We focus on the flow velocity field in the orifice area and the resulting flow-induced forces on key surfaces, as they might impair the comparability between hydraulic and pneumatic flow in the complex geometry at hand. The simulation of the pneumatic flow exhibits supersonic speeds downstream of the orifice at high pressure-drops for small valve openings. At larger openings, the pressure drop and in turn the velocities decrease and the flow is subsonic. Using pneumatics, a positive force is exerted on the spool edge, pushing the spool downwards and opening the orifice. For hydraulic flow, the opposite is the case. These effects persist across all spool strokes to various intensities and can be explained with the flow profiles. Although the pressure differences at the spool edge are significant, the small area on which they are exerted prevents any large forces that might significantly alter the spool position from being developed. Therefore, the flow forces do not prohibit pneumatic substitution of hydraulic testing.