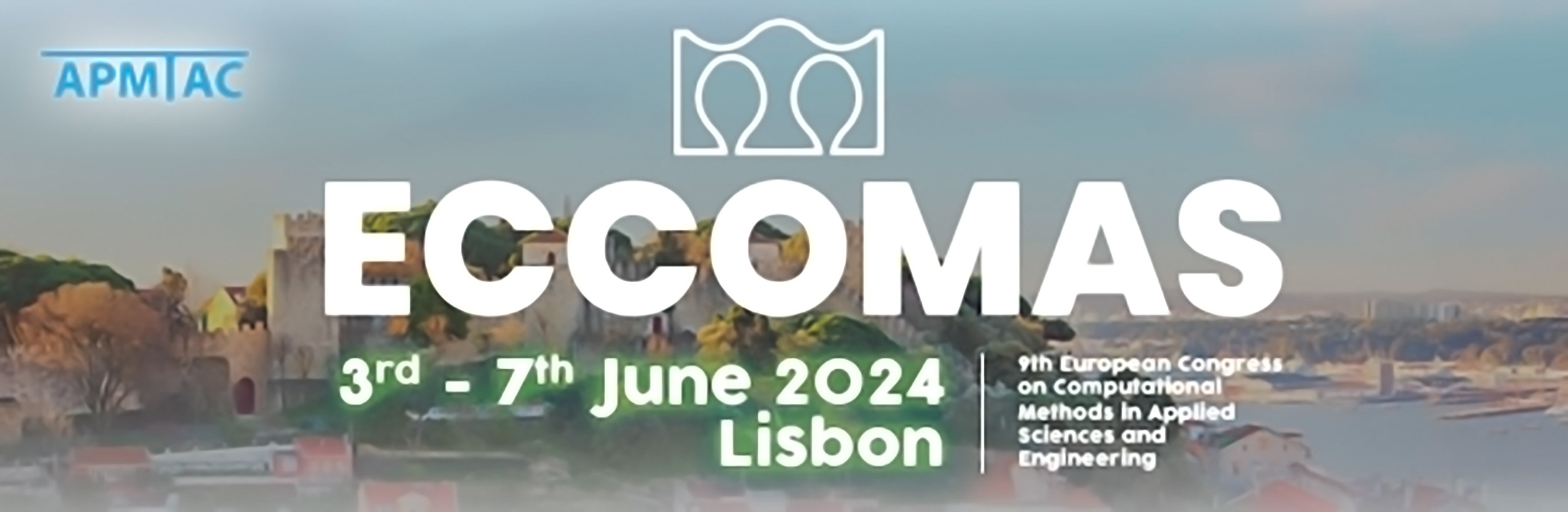
Simulation-driven additive manufacturing within the aerospace industry
Please login to view abstract download link
Additive manufacturing technologies are gaining popularity within the aerospace industry. Among them, Directed Energy Deposition (DED) presents several advantages, such as localized deposition and printing of large parts, which makes it an excellent candidate to replace traditional manufacturing methods. Aircraft engine components produced using casting or forging sometimes see up to 80% of the raw material machined away to produce the final geometry. Layer-by-layer near net-shape deposition using metal wire or powder can be used to decrease the raw waste material and energy use during production. This significantly cuts emissions and mineral resources consumption and reduces the environmental footprint of the component. To be able to introduce DED on flying components it is important to have control over the deposition process and to ensure that the deposited material meets the strict requirements of the aerospace industry. The DED process presents several challenges, including selection and control of the process parameters and final part distortions. In this context, modelling and simulation methods are used to increase the understanding of DED. Understanding the effect of process parameters on the produced microstructure and material properties is critical to building a part of good quality. Modelling of the local melt pool behavior is used to comprehend how individual process parameters affect the process quality. This method enable simulation-driven design of process parameters using optimization procedures. Distortion of the additively manufactured part occurs due to the melting-deposition-cooling cycles during DED. Transient thermo-mechanical simulations are used to understand the effect of the process on the material behavior and stress state at small scales with high fidelity. For large-scale components, an alternative workflow using inherent strains has been developed to reduce the simulation time. In this method, the distortions predicted using the transient thermo-mechanical analysis on a subscale geometry are used to calibrate inherent strains. These strains are applied to the full-scale part to predict the distortions resulting from the process and to understand the effect of the fixture on the part conformance. These different modelling methods enable a simulation-driven design of the DED process from idea to final component.