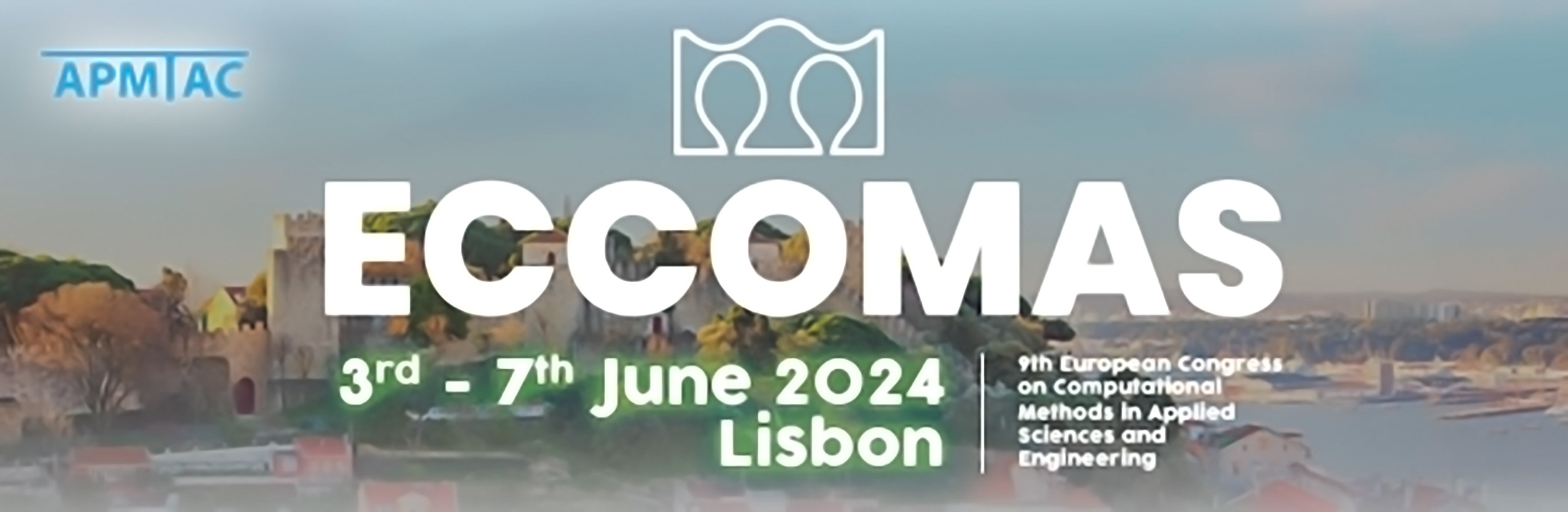
Physical model of the assembly of weld bead’s cross-section geometry through wire arc additive manufacturing
Please login to view abstract download link
Metal additive manufacturing (MAM) process has shown a very strong interest in academic researches as well as industrial applications. Among these manufacturing processes, wire and arc additive manufacturing (WAAM) is very popular because of advantages in rapid manufacturing of medium and large-scale structures [1]. The present work is carried out in the framework of the exploratory project [2]. The project is preceded by the WAS project [3] which is based on WAAM process. The process is relied on an automatized welding process in which a part is built by successively deposed metal weld bead. It has been shown that We propose a physical model for the assembly of the weld bead cross-section geometry. A weld bead cross-section geometry can be simulated using the equilibrium between the hydrostatic pressure and the capillarity force, under two-dimensional hypothesis. This equilibrium can be described by the Young-Laplace equation. At the tri-phase point, the Young equation is used to balance the surface tension forces [4]. It has been experimentally demonstrated that this model can correctly describe the weld bead cross-section geometry on the inclined support [5]. In this work, we extend the physical model for the deposition of the weld bead on the smooth support that describe the assembly of the weld bead. The experimental profiles of a one-weld bead walls, juxtaposition weld bead parts and a thick wall are used to validate the proposed physical model.