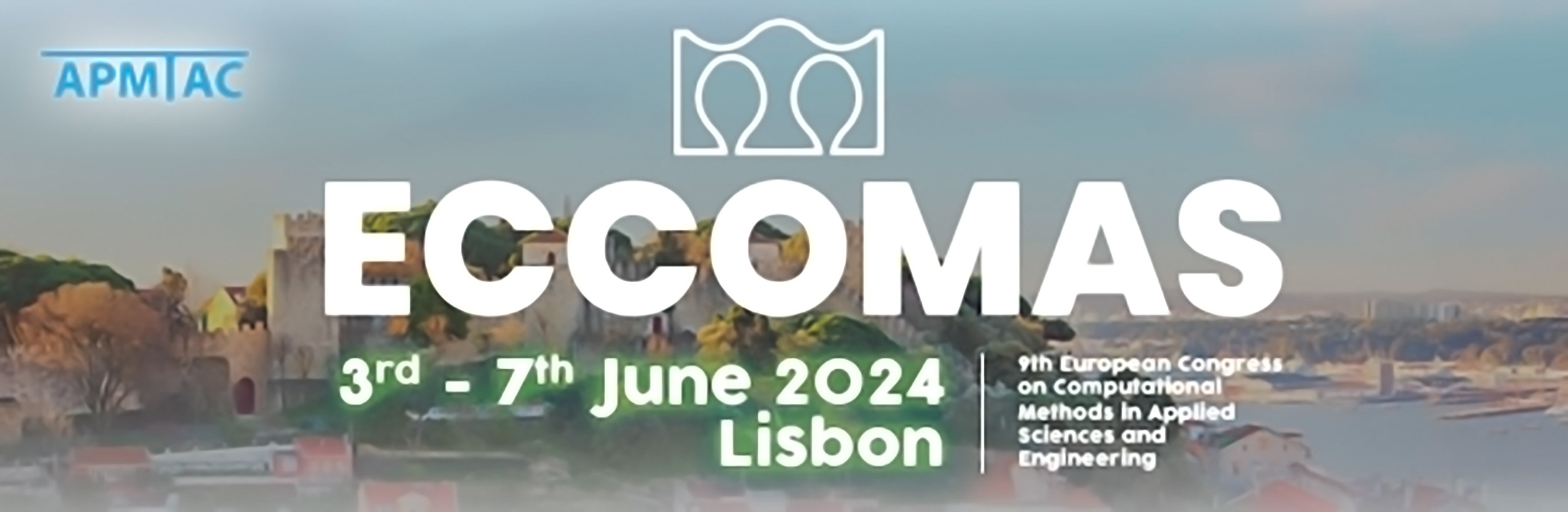
Comparing a novel analytical tool with an established numerical method for use in the initial laminate design of crash structures
Please login to view abstract download link
Energy absorption structures in high performance motorsport and aerospace applications are ever-increasingly manufactured from carbon fibre reinforced polymer (CFRP) material systems. Several new composite materials have been recently introduced to the market, including thin-ply CFRPs and more environmentally sustainable alternatives, such as thermoplastics and natural fibre composites (NFCs). Concerning design tools for crash structures, most of the effort has been directed towards developing Finite Element (FE) modelling approaches. However, their significant computational cost makes these more suited to the detailed design stages. At the initial stages, engineers are still faced with the difficult task of material and layup selection, and their choices are typically based on personal experience with previously employed materials, thus limiting the possibility of introducing novel ones. In this work we compare the accuracy and computational cost of a recently developed analytical tool with those of a more advanced FE model. Using the same macroscale approach as the FE model, and a common dataset of input energy absorption parameters for a commercial woven CFRP, the analytical tool is tasked with the determination of an initial laminate layup of a standard Formula 1 Side Impact Structure design. The performance target is set equal to the load-displacement behaviour calculated numerically, whose accuracy is separately ascertained through a comparison with previous experimental results [1]. This comparative study aims to showcase the potential of the new analytical tool in the initial design stages of crash structures, before a more detailed analysis is conducted through higher fidelity numerical models.