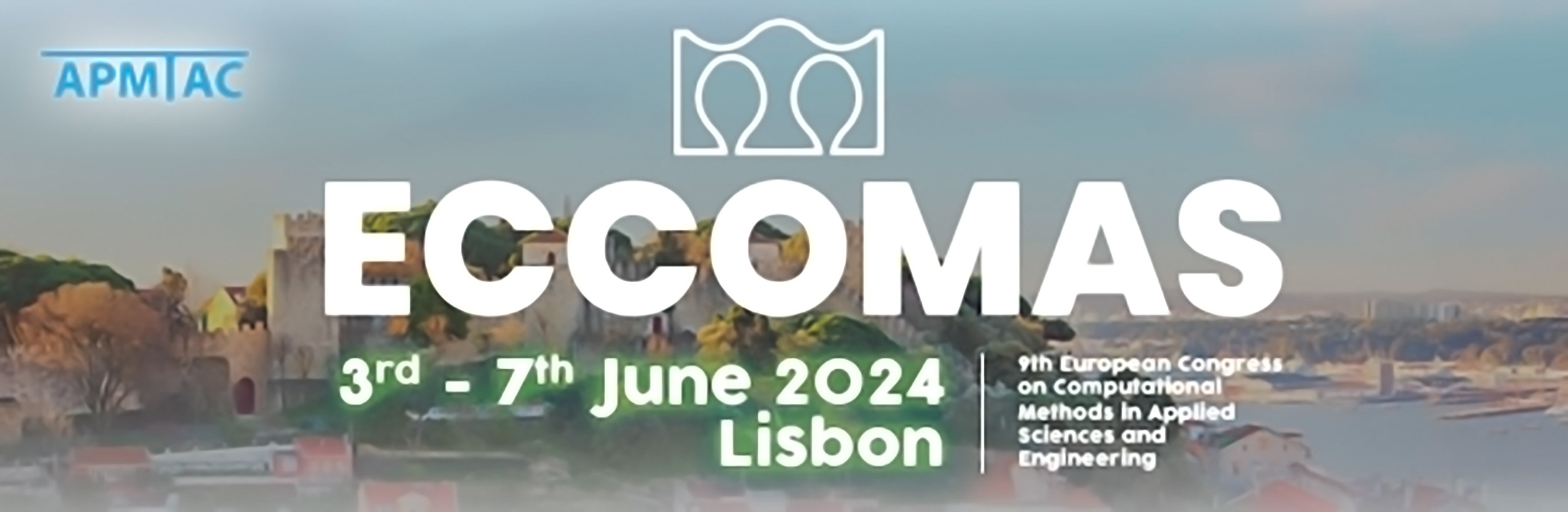
Adaptation of a two-way coupled CFD-FEA model for fire determination of insulated sandwich panels using the Immersed Boundary Method.
Please login to view abstract download link
Structural integrity for cladding products is a key performance parameter, especially concerning fire performance. Building façade products such as Polyisocyanurate (PIR) based sandwich panels are tested rigorously, in line with industrial standards. High integrity panel performance in the event of fire is a vital part of building safety and physical fire tests are used as the basis of product certification that can then be used to ensure compliance with the Building Regulations. However, large-scale fire testing can be costly and time-consuming and so, although it is not a substitute for physical testing within the design process, numerical modelling can provide more understanding of the performance of sandwich panels early in the design cycle, allowing engineers to eliminate poor-performing designs. Fire is an interdisciplinary problem as it is a thermal-chemical reaction that behaves fluidly and impacts structural integrity. An analysis using Computational Fluid Dynamics (CFD) and Finite Element Analysis (FEA) is needed to capture all aspects of a fire performance test. A two-way coupling method is used in this work to update the thermal and structural changes caused by the fire's behaviour. , a two-way coupling methodology has shown to be successful. The method includes coupling an incompressible, Low Mach Number Approximation Method fluid dynamic solver and a Dynamic Implicit FEA solver. However, the software has been shown to have shortcomings when replicating an industrial standard fire test due to its current failure and structural update model. The oversimplification of removing large areas at once can lead to accumulative errors due to structural behaviours not being considered within the FDS model until the steel region has failed. To accurately model the structural changes of the panel, specifically at the joint regions, the author proposes to implement a new structural update methodology to be able to take into account the smallest of changes within the FDS solution throughout the simulation. The method consists of utilising a beta Immersed Boundary Method (IBM) scheme to implement structural changes of the panels within FDS’s cartesian mesh. With each iteration of the two-way coupling, the structural changes are accounted for within FDS. Comparative studies are made between the numerically generated data and a historic industrial standard fire test Tata Steel UK has completed.